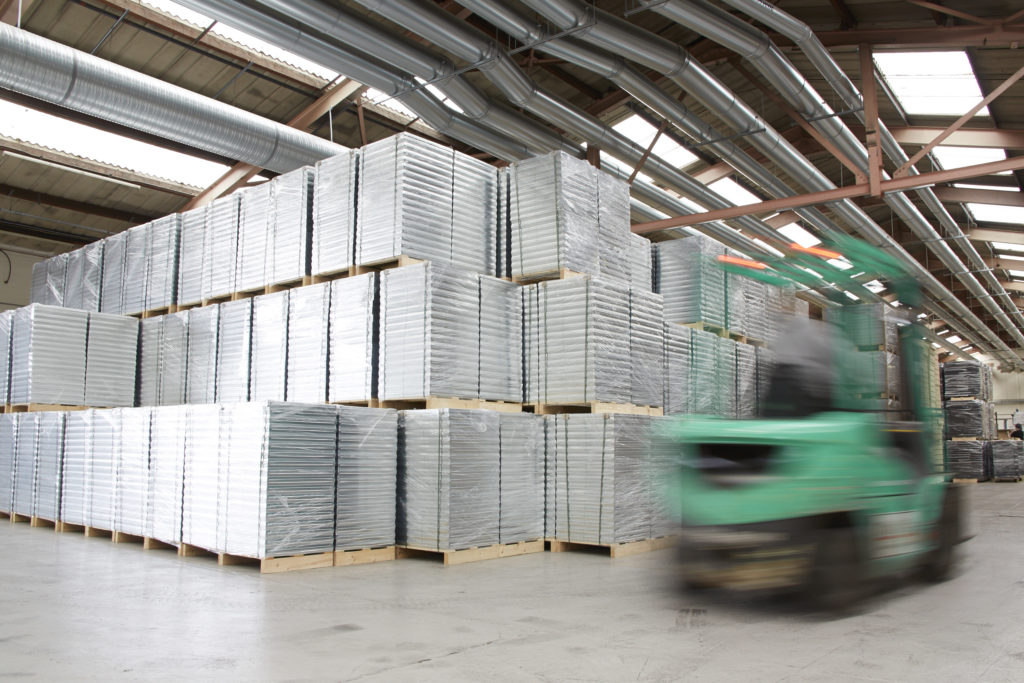
Bathgate Flooring know we have to make certain that the right materials are delivered to the right site at the right time and on the right vehicle. This takes close work between our employees and this is how they do it.
Once the contract is agreed, all relevant information regarding the order including required delivery times/dates and any site restrictions are collated into a Schedule. This Schedule is the trigger to enable organisation of the logistics. A ‘vehicle pallet checker’ is used to check what quantities and weight can go on the vehicle and ensure the optimal vehicle choice.
We begin by creating the ‘Call Off’ which is the total of all materials required and included in the order. The Call Off is split into a number of deliveries to accommodate the total the quantities calculated on the Estimate/Tender Callidus drawings. This way we can optimise the number of deliveries for the benefit of saving costs and reducing emissions via transport. The total materials are then allocated to specific deliveries in line with the agreed Programme and sequence of the works.
This schedule is then shared within Bathgate to ensure that products are manufactured in time and prepared for despatch. This also allows time for any materials not in stock to be ordered or manufactured, if needed.
As the delivery date approaches, dates will again be reviewed/confirmed. This enables us to manage any changes to commencement dates or sequence of works on site which mean that deliveries have to be put back or changed. Once confirmed Transport can then book the relevant vehicle that is included on the Sales Order.
Paperwork is carefully checked by our packers to ensure everything ready for dispatch.
Orders have a final check on the day of dispatch allowing for a last check of contents before the goods leave the factory.